Mokume gane is a technique derived from ancient Japanese metalsmith work that follows on from the creation of Damascus steel. The craft involves the bonding and forging of different alloyed metals to create a variety of patterns.
Traditionally these patterns showcased organic and woodgrain-like swirls but recent advancements have led to uniformity and tessellating pattern production.
Specialising in mokume gane and Damascus silver, Steven Midgett is a modern pioneer of the craft and one of the earliest metalsmiths to incorporate platinum into his billets – prior to this, mokume gane primarily utilised copper, silver and gold metals. With son Jacob, Midgett operates two studios in the US under the name Steven Jacob.
“I first started working with mokume gane during my apprenticeship in 1973. I was working with a Cranbrook Academy master metalsmith and he taught me how to solder bond silver and copper alloys to make a laminate,” he says.
“When the traditional Japanese forge-fired method was revealed [to me], I began to experiment with small torch-fired fusing kilns that I could use to make small billets for my jewellery. I have continued to experiment and grow my knowledge of metals, bonding and patterning techniques ever since.”
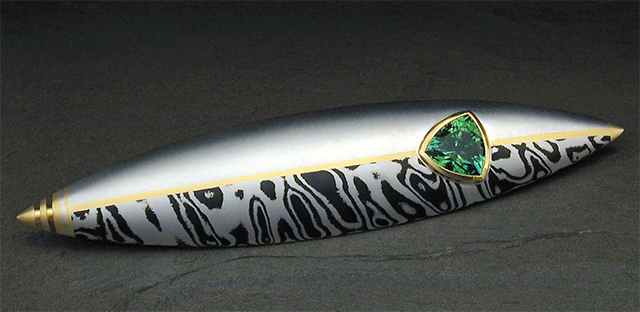 |
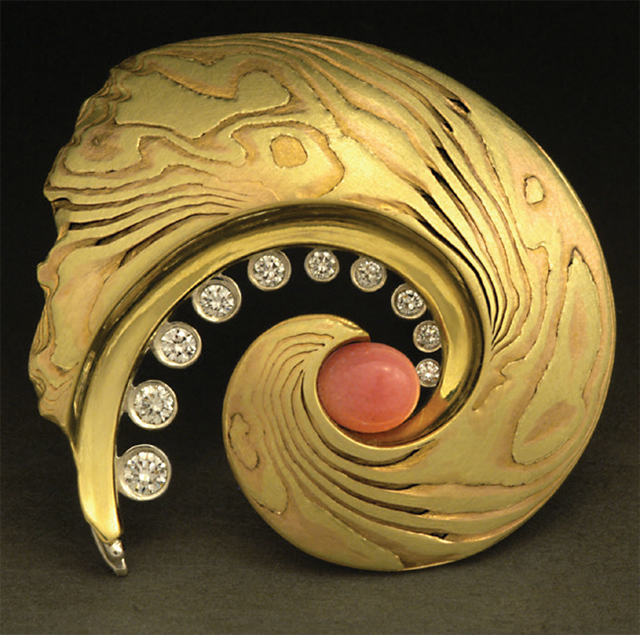 | 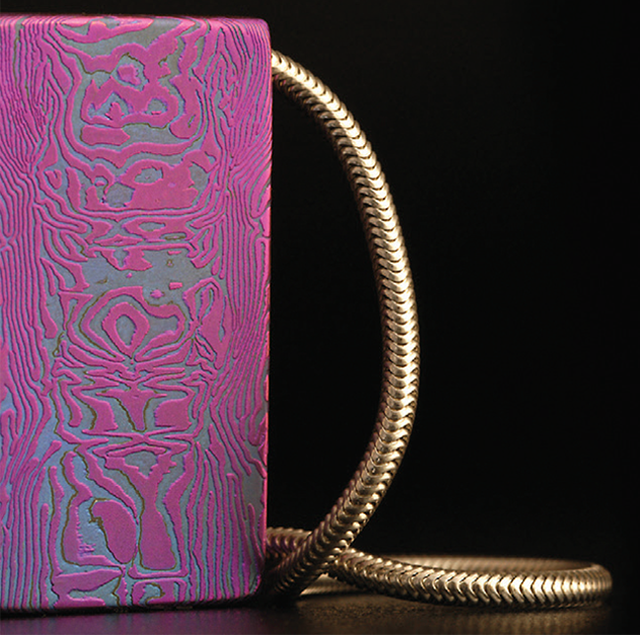 |
Above, below left and below right: Steven Jacob Jewelry |
On the local scene, Hobart jeweller Metal Urges has been producing mokume gane wedding bands for clients who often become repeat customers after falling in love with the traditional woodgrain-textured appearance. Manager Chris Hood says it took much trial and error to perfect the craft, which required great monetary investment to master the soldering of different alloys in billets.
“First, you need a decent jewellery workshop and a sharp mind to work through the process. Secondly, you need to have disposable income and the will to spend it on learning. If things go well, you get some of it back eventually,” he says.
“We went straight in the deep end using 18-carat gold and platinum group metals. The education we got was more expensive than most but also the quality of our skills and recipe improved quickly.”
Hood says the tricky part about mokume gane production is the forging of different metals to create quality billets for jewellery production and says producing billets without side effects takes time and patience.
“Our first billets where fire-fused and were rubbish quality with lots of de-lamination – we were dropping 20 to 50 grams of gold and platinum into refining every two days. Fortunately, once everything was running smoothly with a decent rig and process in place, consistent high-performance billets helped us to win back past losses,” he says.
Midgett agrees that consumer interest makes up for the losses incurred when learning the technique but warns that much raw material is inevitably lost in the laminating process.
“Since almost all mokume billets start out as a flat, parallel-layered laminate, much of the metal needs to be cut away to expose an interesting pattern,” he explains. “It is not unusual to grind and carve away 50 to 70 per cent of the raw metal with which you started.”
For this reason, Midgett believes jewellers need to commit themselves fully to the style to make it work: “Not only does mokume gane require an investment in materials but it is also not a technique that can be used casually. There are so many things that can go wrong or degrade the final product if care is not taken so you have to spend the time to educate yourself and practice your skills.”
Midgett says there are suppliers who produce laminated mokume sheet, wire and plate that can be purchased and then patterned in-house. While this doesn’t offer jewellers an opportunity to hone their billeting skills, it does provide an entry point for pattern production.
“Jewellers can create original designs but don’t have to invest all the time to learn how to make their own billets. Ultimately, making one’s own billets gives a craftsman the most control over the final product but it requires the largest commitment as well,” he explains.
Hood agrees there is more than one way to get involved in producing mokume gane jewellery and emphasises that there are manufacturers willing to share their techniques to market the small field.
“We went with the ‘How hard can it be?’ model and taught ourselves the process but there are all sorts of books and videos available,” Hood says, adding, “We took and tested the ideas we thought best and then built our own custom ‘Frankenstein’ rig and process.”
Hood says it is possible to purchase a US rig; however, with prices sitting around $100,000, this is another expense for manufacturers. While it is a hefty investment, Hood believes a rig does result in more consistently-successful billet production.
“A quality rig and skills all equal fewer variables and a higher success rate. It has been over a hundred billets since we had a problem,” he says.
When asked why mokume gane customers often return to purchase more of the product, Hood believes it stems from a primal desire for natural-looking patterns in jewellery.
“It seems that we are drawn to organic patterns, which is something that mokume gane can do in spades. We have a solid mokume gane client list and our repeat offenders really push us to create more and more unusual and challenging wpieces,” he says.
Certainly, the uniqueness of each finished piece is also particularly appealing to consumers.
“No two rings are identical,” Hood adds. “We all love something unique and just for us.”