The past 10 years have brought about remarkable advances in science and technology.
In 2012, the discovery of the Higgs boson was made public. In 2019, the first image of a black hole was captured while the most notable influence on society has undoubtedly been the rise of smartphones and the impact of social media.
Advances in science and technology have also reshaped a number of retail industries.
It’s been a significant period of advancement for the use of technology within the jewellery industry, particularly when it comes to Computer-Aided Design and Computer-Aided Manufacturing (CAD/CAM).
Jeweller published its first report in June 2012 on the state of CAD/CAM within the Australian jewellery industry.
“The Australian jewellery industry is three to 10 years behind the rest of the world with its implementation of retail computer-aided design (CAD) systems, which has partly been due to our smaller market and the exclusion of global competition,” the report stated.
“It’s futile to ignore the foreign invaders any longer because retailers who work with technology can deliver quality productions in less time with more competitive pricing than their competitors.”
At the time, the question on the minds of retailers was whether or not CAD/CAM would become a significant ‘force’ in the jewellery industry.
Would it make a lasting impact on the trade, or come and go like so many other ideas once entertained as revolutionary?
It didn’t take long for that question to be answered. With manufacturing costs shrinking with each passing year, the industry has increasingly embraced technology which has showcased increasingly user-friendly functionality and cost-effectiveness.
Boutique Comeback
The Pallion Group is the largest precious metals services group in Australasia with manufacturing facilities located in Melbourne, Sydney, Hong Kong and Shenzen
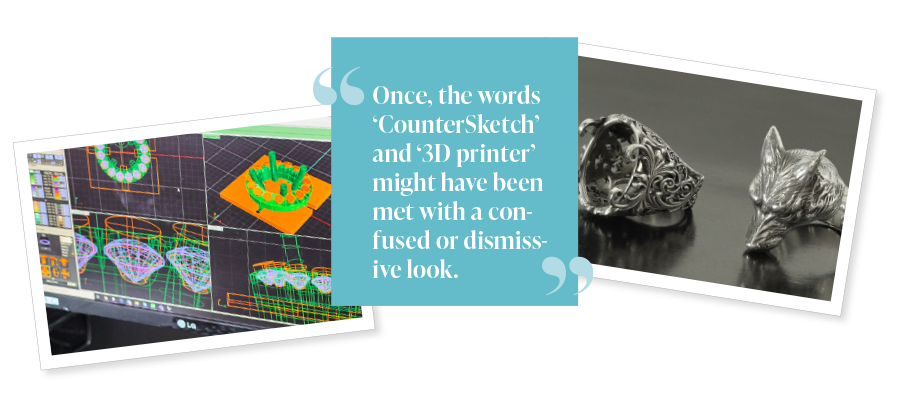 |
Left to right: Palloys was one of the first Australian countries to embrace CADCAM; Intricate designs created by Palloys. Image credits: Palloys |
Since the 1950s, Palloys – one of six entities which forms the Pallion Group – has taken pride in the expansion of jewellery casting, custom jewellery production and CAD/CAM services on offer.
Palloys was an early adopter of CAD/CAM and in 2012, was one of the first companies to share insight with Jeweller on the rise of the technology in the jewellery industry.
Ten years ago, head of operations, Manuel Kalergis, had this to say about the future of the trade.
“You’ll see CAM wax printing getting smoother and turnaround times for CAD drawing reduced,” Kalergis said.
“In the next few years, you’ll also see the rise of Direct Metal Laser Sintering (DMLS) an additive rapid prototyping process that builds up metal using a laser.
“The laser fuses powdered metal layer by layer by scanning cross sections generated from a CAD file. DMLS technology bypasses the casting process all together and will produce stronger products, comparable to CNC manufacturing.”
One decade later, Palloys operations manager Chris Botha says those predictions were close to the mark but not quite in line with what was to come, showcasing that advances in technology aren’t always linear.
“Interestingly, the improvement we foresaw in CAM wax printing seems to be more observable in resins. Resin machines have become exponentially cheaper over the past 10 years,” he says.
“Moreover, casting processes have greatly improved, facilitated by keeping our hardware up to date and of the highest quality.
“Additionally, vacuum-vibration technology and overpressure technology have also improved. Direct Metal Laser Sintering (DMLS) has not dropped in cost enough yet to become accessible in the mainstream market, but we anticipate this will happen over the next 5 years.”
Palloys is currently investigating an investment in DMSL technology.
CAD/CAM has been lauded as a way of bringing ‘in-house’ manufacturing back for jewellers.
Botha says that remains one of the most promising aspects of the trade.
“I am starting to see more of a boutique industry for CAD/CAM in the coming years,” he says.
“Previously, the industry demanded workshops of hundreds of people, whereas now some workshops only require a single person, with their own printer and doing their own work.
“Even if just for prototyping, the CAD/CAM industry is becoming a more accessible industry.
“The CAD software industry is moving towards a future where consumers have greater control and autonomy. With the constant technological evolution, now there are many more user-friendly, lower-cost options available for users in terms of 3D Printers.
“There will be an amalgamation between the handmaking jeweller and the CAD designer, moving forward. We have already begun observing this trend in our own client base.”
Rapid Prototyping Services production manager Ben Farago agreed with this sentiment but says that for those exploring CAD/CAM production for the first time, it’s crucial to avoid the common pitfalls.
“I think everyone in the trade knows the general direction things are heading in the future, the advancements have been steady and consistent,” Farago says.
He also emphasised the importance of research and forwarding planning when it comes to production.
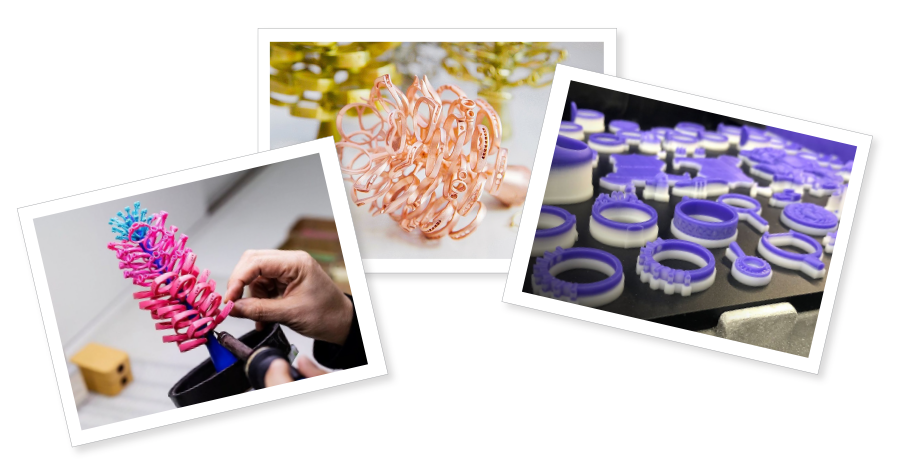 |
Left and middle: Sprue trees created by Palloys as a part of the casting process.Image credits: Palloys Right: Models created using 3D printing by Morris and Watson. |
Chemgold
Based in Sydney, Chemgold aims to offer the solution to any jewellery manufacturing dilemma - by offering all precious metal products and services; casting, refining, fabricated alloys and mounts paired with a catalogue consisting of thousands and thousands of designs.
Chemgold was a notable contributor to the 2012 CAD/CAM report. At the time director Larry Sher highlighted the opportunity technology presents jewellers when it comes to avoiding expensive local labour costs: “There are far more opportunities for jewellers to be able to create whatever they require.”
He added: “Chemgold has exciting developments in the pipeline and aims to be a leader in the development of new technologies for the jewellery industry. Advances in technology are increasing at a rapid rate, which will only improve the speed and resolution.
“To remain competitive, the majority of jewellers will need to embrace CAD/CAM by outsourcing the design aspect to companies such as ours, along with learning to use the software themselves if they choose.”
In the years since that statement, Chemgold has significantly invested in staff training to account for rising demand, with jewellers increasingly utilising Chemgold’s CAD-based libraries.
Today, Chemgold’s director Darren Sher says he continues to be impressed by the rapid rate at which the industry adopts advances.
“I believe that CAD programs will become more and more user friendly,” he says.
“We’re going to see printers reach higher resolutions and faster printing. There will inevitably be developments in software for job tracking for the customer too. Providing a client with up-to-date information on the status of an order in the manufacturing process is highly valued.”
With the increase in popularity of the technology Sher says there is always a need to train and hire staff to service demand and services.
“We are also continuously building on our database for our staff to ensure any [updated] information is easily accessible.
“With jewellers and stores, in general, being extremely busy we have found that using a one-stop-shop for CAD/CAM suits many of our customers who can use all or some of the services for jewellery production – from designing, printing, casting, moulds, finishing and setting.”
World of wax
One name we may soon be hearing more often is Riacetech. The business was founded in 2006 by Giovanni Lejkowski and is based in Arezzo, a city in eastern Tuscany in Italy.
Riacetech creates innovative wax injectors which provide companies in the casting industry with a range of functionalities and compatibilities.
Technical sales engineer Alessio Farnetani told Jeweller that what’s capable today with wax injectors would have been considered fanciful a little more than a decade ago.
“Our wax injectors were first created in 2006 and the business was started in 2007. Today, what we are capable of producing with the injectors, it was the stuff of dreams back then,” he says.
“A lot of the advances come down to things like network connectivity and improvements in user-friendly access. Today, it’s very much easy to begin making creations compared with what it was like not too long ago.
“Improving user experience has always been important for us, as is increasing the efficiency of use, both to cut down on waste in an environmental sense and also to save money for the creator financially.”
Riacetech serves clients both in and out of Europe, with a number of Australian businesses currently utilising the company’s wax injectors.
Farnetani says that his sector has undergone a rapid rise and fall in orders since the ‘conclusion’ or winding down of the COVID pandemic.
“For our business, the flow of orders we’ve had in recent months, I would describe as sort of like an elastic band,” he says.
“Everything of course slowed down to a halt during COVID, and then when business resumed everyone rushed to get their orders in and we were very, very busy.
“Now we’ve completed that surge of orders and things have dried up again somewhat, but we’ve completed our projections for the remainder of the year and our outlook is positive and we’re confident we’re heading in the right direction.
“I can’t speak for everyone, of course, but I think that’s been a common experience for a lot of engineering businesses such as ours.
The company is expected to showcase its products at the upcoming Sydney trade fair, and Farnetani says he hopes to gain some long-term Australian clients.
“Because this industry is always advancing and improving, it’s never a one-and-done type of thing with our products, the newest improvement is always right around the corner,” he explains.
Lessons learned
Rapid Prototyping Services, based in Sydney, also works with wax – offering printing and casting services along with CAD/CAM manufacturing of precious metal products and 3D printing.
Farago told Jeweller that last year’s pandemic and the restrictions on public gathering highlighted some important trade principles, such as the value of an up-to-date and user friendly website.
So, what does the future hold?
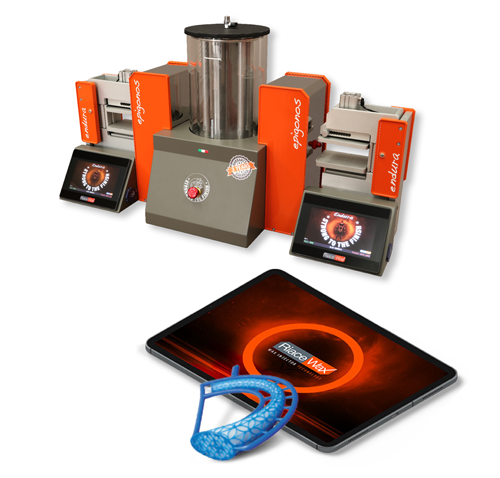 |
Above: Riacetech's Bi Hydro Endura is controllable from a colour touch screen, and is able to produce about 480 3D hollow pieces of small and medium size each day. Right: Creators use a touch screen interface to operate the injectors. Image credits: Riacewax |
Over the past decade, the largest change in the CAD/CAM industry has been the reduction of cost required to utilise manufacturing technologies.
A method that was once restricted to the largest of companies quickly opened up as technology evolved, and new, jewellery-specific products and programs arrived on the market.
The Jeweller 2012 report forecasted these changes and concluded with an urgent call to retailers.
“CAD is growing quickly. With this sort of technology around the corner, how can retailers ignore it?” the report asked.
“The future of everyday-CAD is almost here and grows closer by the day. When toy companies like LEGO, and furniture conglomerates like Ikea, are already developing CAD-based software for the everyday user, it’s obvious that something big is just around the corner.
“So, what does the future hold?
"Retailers who choose to embrace CAD technology as a part of their forward planning will benefit greatly from this shift in the way that consumers buy jewellery just as retailers who choose not to embrace it will stay exactly where they are.”
According to Palloys’ Botha the industry at large has heeded this message.
“The acceptance and adoption rate of CAD/CAM jewellers has been extremely high. At this point, most companies use CAD and CAM – this has exceeded my expectations by far,” he says.
“CAD/CAM has bought a whole new level of people into the industry; for people who previously did not have the resources or the skillset, CAD/CAM gave them the opportunity to express themselves.
“There has been widespread uptake of CAD/CAM services.
"At Palloys, we had customers who came to us with no knowledge about CAD/CAM services, but just with a dream of seeing their drawing or idea brought to life.
“It has given the trade a newer, more interesting life, as these designers challenge the status quo.
Chemgold’s Sher echoed this sentiment and says that Australia’s attitude towards technology in jewellery manufacturing in particular has improved in recent years.
“We believe that with the what has unfolded during the pandemic, mostly regarding the freight, but, also the quality and after-sales issues that occurred during that time, a lot of manufacturers/stores decided to opt for Australian made,” Sher says.
“Not only is it a great selling point for most of the market, it’s also reduced their turnaround time greatly.
"Customers always value something being made locally and delivered much quicker than any overseas competitor.
"The quality and attention to detail have also been a big turning point for most of our customers as they receive the piece they require correctly the first time around in a quick turnaround.
“Apart from this, they also enjoy the benefits of a much higher level of after-sales service.
“We have seen a mass number of manufacturing roles open in the industry the past few years with jewellers and setters and CAD designers being in high demand across the country.
"This shows that there is a lot more interest in bringing manufacturing back to Australian shores and keeping it here.”
From the time of the first Jeweller CAD/CAM report until today, a remarkable amount of industry advancement and change has occurred.
With costs continuing to decrease and capabilities continue to improve, the next decade appears primed to create manufacturing possibilities that a jeweller today would believe is a mere fantasy.
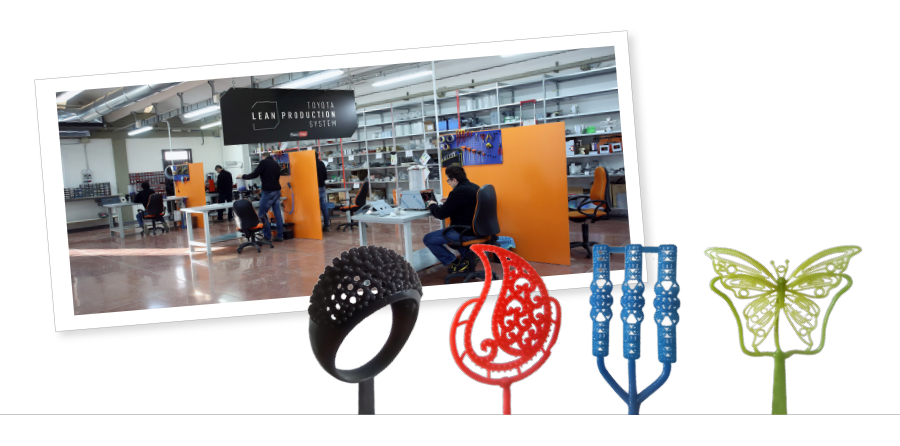 |
Left to right: Riacetech introduced lean production systems with the aim of eliminating waste; Wax moulds created by Riacetech. |
Best-known for its use in motion-capture for films and TV, as well as medical prosthetics manufacturing and robotics, 3D scanning is increasingly being applied to jewellery in order to generate digital models of real-world pieces.
Some of the most common applications include scanning unusual engagement rings to design a perfectly flush wedding band, creating accurate settings for fancy-cut gemstones, and replications of existing jewellery.
The technology is also useful for jewellers who wish to keep 3D files of stock for insurance, record-keeping, and valuation purposes, or to identicaly replicate a customer’s jewellery, should the original be lost or stolen.
In terms of design, Stuller’s Montgomery names MatrixGold as the “mainstream CAD software for the serious CAD designer worldwide”, calling it “the most effective jewellery design software on the market”, suitable for designing completely custom pieces ready for printing and casting.
At Palloys, jewellers can create a custom design from scratch via the Palloys.com platform or upload an STL file with their design. The Palloys Design team is also able to create custom renders for jewellers to use as a sales feature: “Bringing a life-like element to the design is an imminent part of the selling process. Rendering in the modern age is of such a quality, it could almost pass as life-like,” says Botha.
Looking to the future of CAD/CAM, Tok believes small improvements will likely continue until the next “giant leap forward” – direct 3D printing in precious metals.
Chemgold’s Larry Sher agrees, noting, “We are constantly looking at new technology such as direct-metal printing. This could also be an option in the near future if it becomes economically viable. Currently the machines are extremely expensive to run and the quality is not at the standards required.”
From the days of sketches and handmade models to 3D scanning and direct metal printing, CAD/CAM reflects the changing nature of the jewellery trade as well as the rapid pace of change across all industries and ways of life.
*CORRECTION: An earlier version of this article attributed the wrong quotation under a picture of Mr Darren Sher of Chemgold. While the comment was correct, Mr Sher did not make it.
read emag