As the saying goes, a workman is only as good as their tools. Like most industries, over the years jewellery creation has evolved from largely hand-based, physically-taxing equipment towards more efficient technological solutions – allowing for ever more precision, design creativity, speed, and fewer injuries on the bench.
Manufacturers – and even jewellers themselves – have taken inspiration from other industries such as car manufacturing and welding to develop new, or refine existing, tools.
Selwyn Brandt, director Australian Jewellers Supplies, tells Jeweller, “Minor innovations happen all the time. People try and improve on basic hand tools – the hand skills that are required of a jeweller still make use of traditional tools, such as pliers, hammers, files, so on.
“Many improvements to these occur because a given jeweller, somewhere around the world, determines that the tools that are available just aren’t enough so they then design their own and many of these tools often end up being available to the wider jewellery community.”
He points to aluminium saw frames – which are more balanced than older models, helping to prevent repetitive stress injuries – and precision hammers for setting work as examples of such equipment.
Brandt adds, “Other pieces of equipment are taken from other fields and modified so that they are usable in the jewellery industry – usually ‘toned down’ and miniaturised.”
In watchmaking, Catherine Craner, managing director The Battery Man, says the focus is on innovations and refinements from established brands with a reputation for quality and reliability.
“For the essentials, watchmakers turn to manufacturers like Bergeon, which was founded in Switzerland more than 200 years ago, Beco Technic from Germany, and Seiko in Japan, which all have a reputation for very high quality. Any new innovations from these manufacturers can be trusted.”
Meanwhile, the technology sector continues to provide innovative tools for jewellery businesses, from e-commerce to billing and workflow management.
Best of the bench
When it comes to jewellery manufacturing, two forms of micro- welding have been rapidly embraced: laser and pulse-arc.
Pulse-arc welding joins metals through the fusion process.
“Pulse-arc welding creates a very instantaneous and low-heat spark between two bits of metal which creates a fusion,” explains Brandt.
“This can also be used for unrelated metals, precious metal or non-precious metal and there is a version that is used for very hard metals in the dental industry.”
He adds, “Fusion is an interesting concept because it’s low- heat, non-destructive, and there are many delicate articles we can weld with this technology that we couldn’t do before. Previously, all welding was done using open flame torches.”
Meanwhile, laser welding – used for many years in the broader manufacturing industry – has been redeveloped for use in jewellery, with machines producing a fine, concentrated, heated beam that is ideal for working with metals such as steel, aluminium, and titanium.
At Jewellery Services in New Zealand, director Richard Mayo tells Jeweller, “We have just purchased our fourth laser welder unit. They are amazing for speed; we use them for most chain repairs and any claw work.
“We also use them for platinum sizing and will be purchasing a camera/screen system for one of them for training purposes.”
Laser technology is also used for engraving, with Mayo adding, “We have started using a new laser engraver, which is great added-value for the retail stores we support.”
Alongside laser engravers, pneumatic engraving and stone- setting machines, such as those produced by GRS, remain popular among jewellers.
“The Graversmith system is 30 or 40 years old, but the manufacturer, GRS, is a very progressive company and they continuously introduce innovations and subtle improvements to each of their models over time,” says Brandt.
Notably, Brandt points to the use of microscopes as a more recent innovation in engraving and micro-setting.
“Using the microscope, together with the necessary amount of light, has made a big difference to the ability to create accuracy in delicate and very intricate work,” he explains.
“The microscope is very important, from that point of view, to give the jeweller that vision and ability to work on small, delicate things, which you cannot really do with the naked eye.”
Jewellery Services currently has two microscopes used for setting work, and plans to purchase a third.
Microscopes are also now frequently used in laser and pulse- arc welding, as jeweller’s microscopes have a built-in welding- grade lens that filters light to protect the eyes – a common concern on the bench.
Polishing and finishing has seen more innovation: “There is some equipment now that uses a modification on what jewellers know to be ‘tumbling’, using electrolysis to polish and finish pieces of jewellery.
“That has been borrowed and miniaturised from other fields, such as the motor industry,” says Brandt.
The dental industry has also made its mark on jewellery with the introduction of micro-motors, which Brandt says have “almost entirely” superseded flexible-drive motors for drilling.
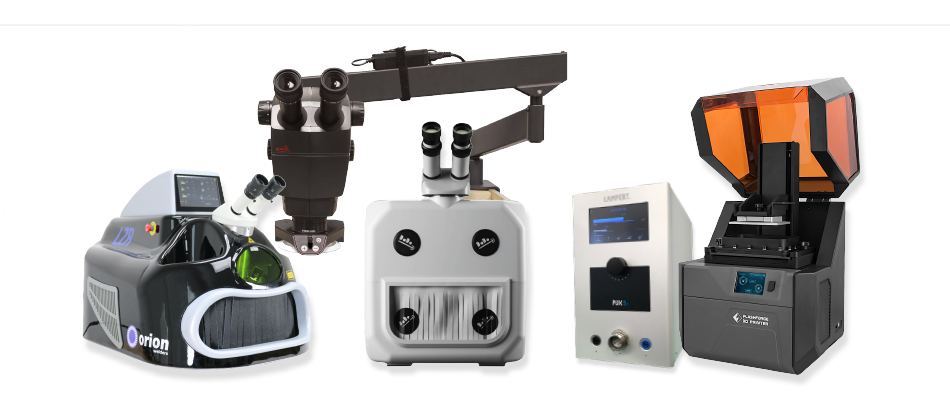 |
Above (L to R): Orion LZR100 Laser Welder; Leica A60 Microscope; Dado Laser Welder, Lampert Puk 5.1 Precision Welder; FlashForge 3D Printer, all courtesy AJS |
Overlooked essentials
Often overlooked, yet essential to any jewellery business, is cleaning technology.
“We have supplied a vast array of equipment to almost every industry in Australia, and the jewellery sector will almost always specify Elma ultrasonic cleaners and supplies,” says Tim Fastnedge, managing director, Techspan Australia.
“The brand is very well known and respected around the planet for their effectiveness and reliability.”
However, noise is a common complaint when it comes to ultrasonic cleaning. To address this issue, Elma has recently introduced a range of sound enclosures.
“Depending on its frequency, ultrasound activity can generate an array of different noise levels within the cleaning liquid,” explains Fastnedge.
“Elma has developed noise protection boxes for a number of ultrasonic cleaner device sizes, which can significantly reduce the noise level. There are three models – two that cover most of the small-to-medium-sized ultrasonic cleaners, and an extra-large size.”
In terms of cleaning for watchmakers, Craner says Elma ultrasonic cleaners are also “very highly regarded”.
“We’ve also heard very positive feedback on the Heli cleaning products from Beco Technic, which can be used on both stainless steel and leather,” says Craner.
“The quality of the cleaning is fantastic, and there are no harsh chemicals in the formula, which is innovative.”
Craner also observes that “a good-quality compass and demagnetiser” are other often-overlooked pieces of equipment on the watchmaker’s bench.
“Magnetic devices are everywhere – smartphones, tablets, and even phone holders for the car which use magnetic docking to keep the phone in place.
“People often don’t realise how magnetism can impact a watch – that should be the first thing that’s checked in a repair, before moving on to the battery or the mechanics,” she explains.
“So, the compass and demagnetiser are essential. Also, non-steel tweezers – you should never use steel tweezers with a watch battery!”
When it comes to innovations, Craner points to “case openers that can cater to the larger watch sizes that are becoming increasingly popular”.
“With the fashion for larger watches, the tools need to be adapted; the Bergeon JAXA case opener, for example, works for cases up to 62mm,” she says.
Craner also notes the new Seiko S880 Digital Multi- Tester, which she calls “a step up from the previous S860 model, which has been discontinued”.
“It’s due to arrive in Australia towards the end of the year and we will be accepting pre-orders at the Sydney trade fair [International Jewellery & Watch Fair],” she adds.
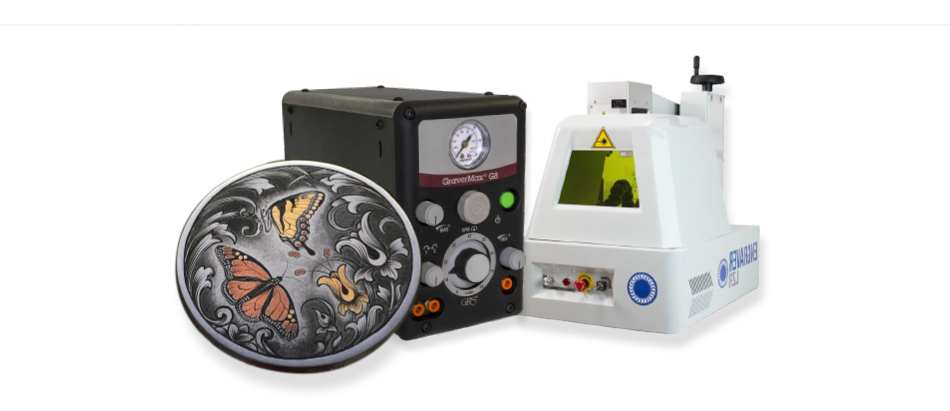 |
L to R: Jake Newell custom hand- engraved stainless steel with gold and copper inlay; GRS GraverMax G8; Orion Nano 20 Watt LZR Laser Engraver, both courtesy AJS |
Technology solutions
Beyond the bench, Brandt says no discussion of jewellery equipment innovation would be complete without mentioning 3D printing and computer-aided design (CAD).
“The big innovation in casting has been, of course, 3D printing, and with that we can create so many more options for jewellery,” Brandt explains, adding, “Jewellers used to literally hand-sculpt the models and they now do this using CAD and 3D print very intricate models.”
Chris Hill, director LST Group, says, “[3D jewellery software developer] 3Design has released version 10, which has 50 new features and 20 new tools; CAD makes it easier for jewellers to quickly turn their ideas into reality.”
Hill believes CAD and 3D printing offer a “significant advantage” to jewellers: “Not only can you significantly reduce production costs, but you can control the workflow, communicate concepts with customers, prototype ideas and deliver a better product in a shorter time.”
He adds, “With CAD, the technology to create and sell online will become more seamless and offer more customer interaction directly on the website– interactive 3D models in a web browser that can be adjusted for metal colour, stone size and shape, updated instantly with a price ready for the customer to order.
“The tools are already available, it will just take a few innovative brands to get their online shopping experience up to date,” Hill explains.
On the supplier side, Palloys, AGS, PJW, Regentco and A&E Metals – all part of the Pallion group of companies – launched an all-in-one platform in 2020 for customised 3D printing orders.
The platform, which took two years to design and implement, allows jewellers to upload a CAD file and receive an instant quote for a finished piece, including everything from print to mould, casting and finishing.
“The instant quoting for CAD files, casting from their own mould library, fabricated metals and diamonds allows jewellers to enjoy accurate and instant quotes they can pass onto their customers, giving the jewellers an instant competitive advantage,” Alison Habbal, assistant operations manager – jewellery at Palloys, told Jeweller last October.
As a result, online orders for the group’s jewellery division more than doubled in 2021.
At Jewellery Services, Mayo tells Jeweller work has already begun on a “customer portal” “where stores can login and see their job information, images, billing, order stock, etcetera.
“We will have this live for Christmas,” he adds.
Digital innovation has also occurred in other areas of Jewellery Services’ business.
“We have recently updated all our computer systems to be cloud-first, using Microsoft Dynamics as our core system,” says Mayo.
“With this, we have been able to develop a way for our jewellers to use tablets to manage their workflow; they take a picture of the item with the tablet, fill in the necessary information, and it goes straight to billing.”
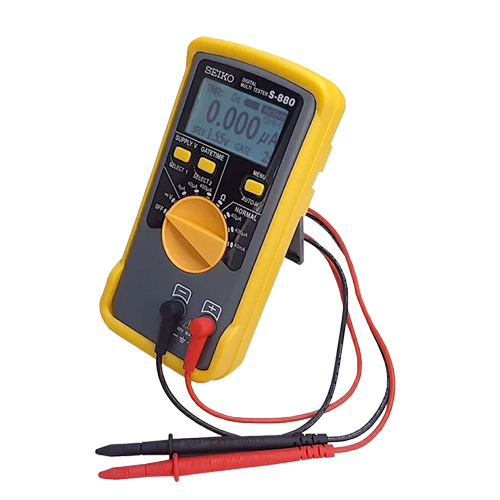 | 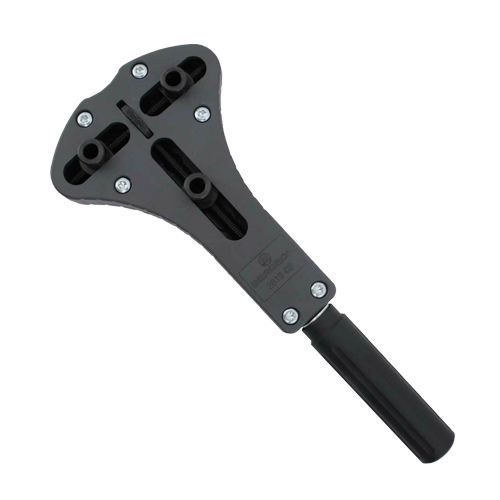 | 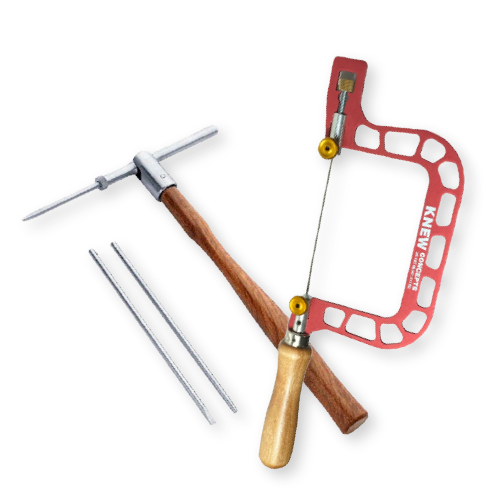 |
Above: Seiko S880 Digital Multi-Tester | Above: Bergeon JAXA Case Opener | Above: Whaley Sliding Hammer; Knew Concepts Aluminium Saw Frame, both courtesy AJS |
Knowledge is power
For retail jewellers looking to embrace technological solutions, Hill emphasises the importance of education. “Many jewellers have been left behind with CAD, although it’s never too late to learn a new skill,” he observes.
Mayo notes that Jewellery Services’ new microscope and laser welder will be fitted with screens and cameras for training purposes.
The critical importance of training is recognised by Katherine Kovacs, federal chair of the Gemmological Association of Australia (GAA).
“Ultimately, tools are only as useful as the jeweller holding them; the education on how to use any piece of equipment – no matter how basic or advanced – is essential,” she tells Jeweller.
The GAA’s courses offer comprehensive guidance on how to use the latest gemmological equipment and how to interpret results – particularly when it comes to correctly identifying gemstones and detecting treatments, which may not have been disclosed.
In June, a spotlight was shone on lab-created diamond detection when the International Gemological Institute (IGI) exposed an 6.18-carat diamond as lab-created, despite being laser- inscribed with a natural diamond’s grading report serial number.
“Identification is crucial for both natural and lab-grown diamonds, as both markets are prospering and important to consumers, and at IGI, we saw that firsthand when we uncovered the largest misrepresented diamond, weighing in at 6.18-carats,” IGI CEO Roland Lorie told Jeweller.
IGI anticipates that the number of lab-created diamonds cut and polished to mimic the characteristics of specific natural diamonds, with grading reports, will continue to increase, which reinforces the importance of secondary verification and proper grading and screening.
“As an industry, we must work together to ensure that we are providing shoppers with accurate identification,” said Lorie.
He added, “The Institute understands the choice consumers have when buying either natural or lab-grown diamonds, and we must communicate with the utmost certainty that their selections are aligned with what is reported on the certificate.”
For retail jewellers, there have also been recent innovations in desktop and handheld diamond detection devices – also known as diamond verification instruments.
Yehuda Diamond Company recently released its Sherlock Holmes 3.0 diamond detector, which retains the previous model’s 100 per cent detection rate of CVD and HPHT stones, as assessed by the Natural Diamond Council’s ASSURE Diamond Verification testing process, previously known as Project ASSURE.
At the same time, several improvements have been made, including a significantly lower false-positive rate, more accessible design, and a new eight-times magnification view.
Meanwhile, OGI Systems’ Diatrue CS is one of the most recent additions to the ASSURE Diamond Verification directory, having been tested in early 2021. According to OGI Systems, it was ranked highest for a novice operator, testing for lab- created diamonds larger than 2mm.
The Diatrue CS includes a diamond reference database, auto- detection of both chemical vapour deposition and high-pressure, high-temperature lab-created diamonds, and improved software from previous models.
Notably, the total number of detectors in the ASSURE directory had risen to 33 at the time of publication – however many require the operator to either fully or partially interpret the results, once again emphasising the importance of equipment knowledge.
Whether manufacturing or retail jeweller, it is critical to maintain not only up-to-date equipment that meets the needs of your business, but also education in how best to utilise the many innovative tools at your disposal.
SPOTLIGHT ON
ENGRAVING
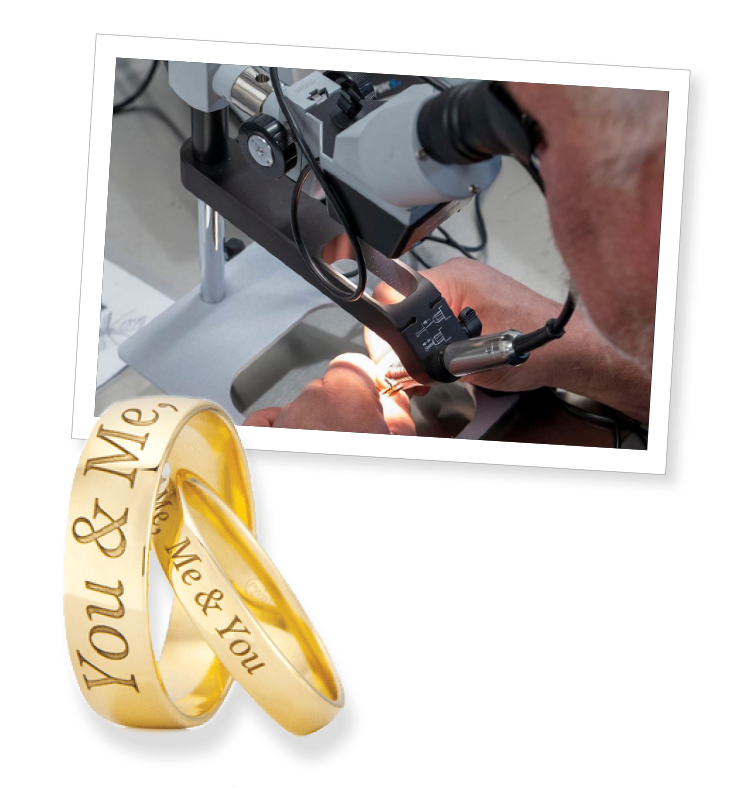 | Above: Hand-engraving with pneumatic tools, courtesy GRS. Laser-engraved rings, courtesy Peter W Beck |
Jewellery engraving has a long history, yet its appeal persists into the modern day – particularly as consumers become ever-more oriented toward personalisation and customisation. Beginning with traditional hand tools and physical force, the art developed over time in order to reduce the stress on the jeweller or craftsman’s body, as well as increase precision and the variety of designs available. Pneumatic tools, such as those developed by US company GRS, were a significant breakthrough and continue to be used widely across the jewellery industry today – both for their affordability and versatility. Such equipment is frequently upgraded with new settings and attachments, and are ideally suited to intricate work. As the technology has evolved from traditional hand tools, many can also be used for gem-setting. Laser engraving developed separately, reaching the jewellery industry after the technology had matured. Using light to alter the surface of the metal based on digital inputs, laser engraving is ideal for replicating fingerprints and photographs, engraving all types of metals, and enhancing the contrast in a jewellery design. However, advanced laser machinery can be expensive – with some models priced in the tens of thousands of dollars – putting them out of reach of many jewellers. Instead, they turn to jewellery services suppliers to create custom laser-engraved designs. |
read emag